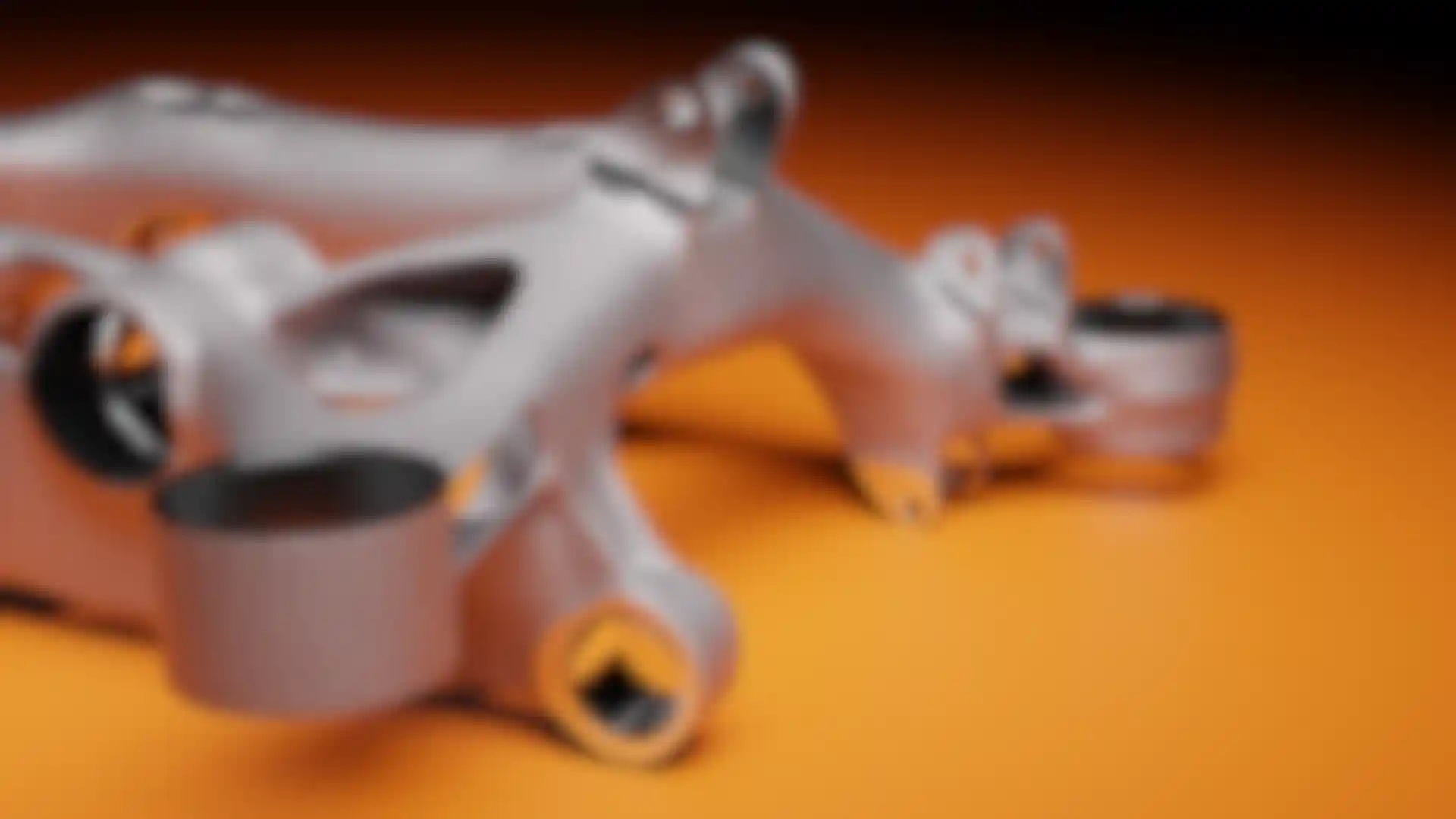
Wie ZBrush Fertigungsprozesse in der Automobilindustrie revolutioniert Bionic Mesh Design setzt das 3D-Tool ein, um Leichtbauteile für die Autoindustrie und andere Bereiche zu konstruieren.
Als talentierter Luft- und Raumfahrtingenieur mit einer Leidenschaft für Leichtbau arbeitete Thomas Spoida im Rennsport, bevor er in die Forschungsabteilung eines Automobilkonzerns wechselte, der seine Ideen zu neuen Materialien und Technologien begrüßte. Leider waren die Veränderungen oft zu kostspielig, um sie umzusetzen.
Dennoch widmete sich Spoida der Erforschung von Möglichkeiten, um den Bau von Leichtbauteilen erschwinglicher zu machen. Schließlich lag die Lösung auf der Hand: eine clevere Topologieoptimierung und Subdivisions, die er mit einer Kombination aus ZBrush und CAD erreichte.
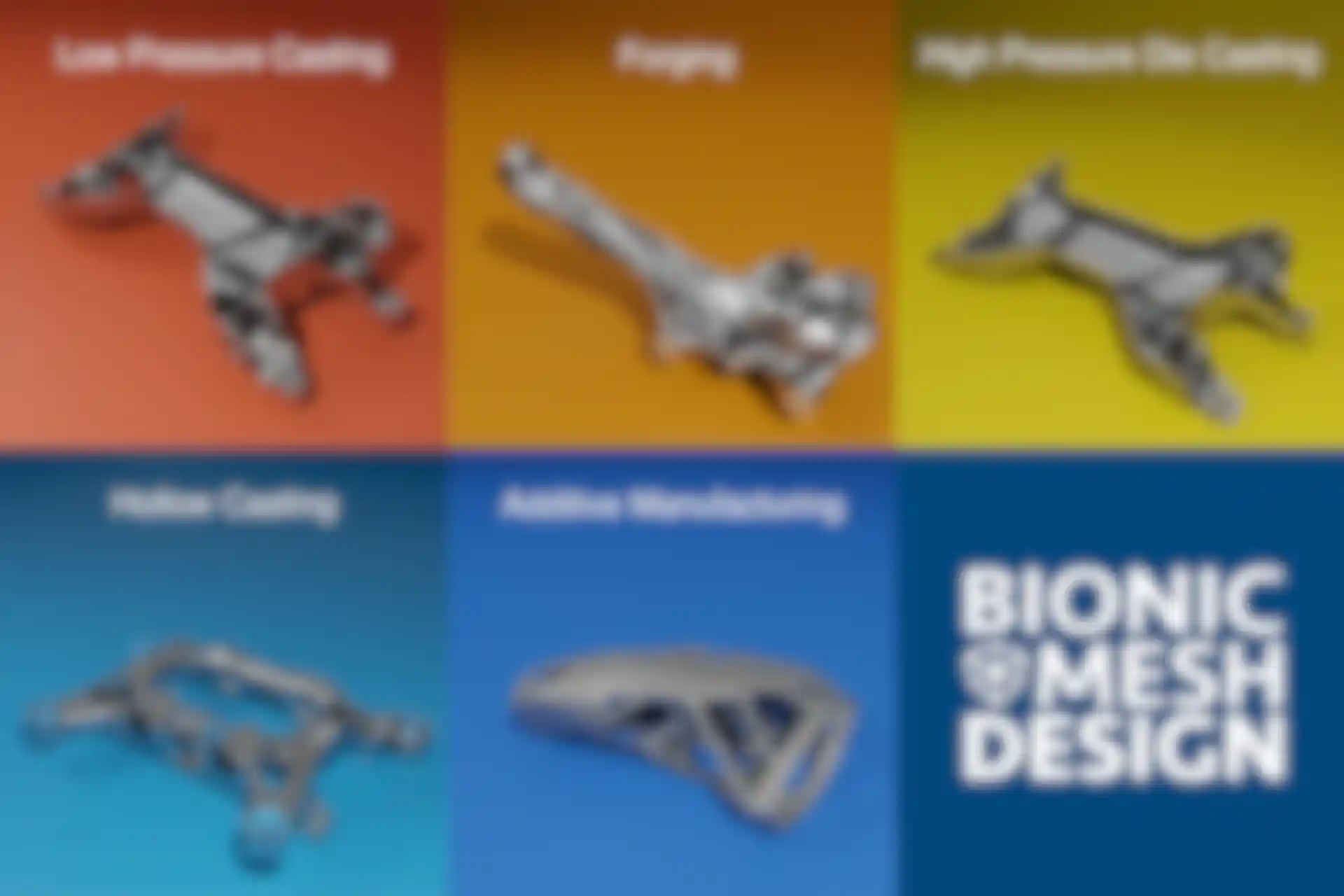
Wir sprachen mit Spoida darüber, wie der Prozess der Umwandlung von optimierter Topologie in herstellbare Geometrie viele Branchen revolutionieren könnte und wie sein Unternehmen, das in Deutschland ansässige Bionic Mesh Design, Leichtbau für alle zugänglich und erschwinglich machen will.
Bitte erzähle uns etwas mehr über dich und darüber, was dich dazu gebracht hat, 2020 dein eigenes Unternehmen zu gründen.
Spoida: Leichtbau hat mich während meines Studiums der Luft- und Raumfahrttechnik fasziniert. In diesem Bereich liegen die Vorteile des Leichtbaus auf der Hand: Ein leichteres Fluggerät, sei es eine Rakete oder ein Flugzeug, kann mehr Last tragen und/oder hat eine größere Reichweite. Es gibt verschiedene Materialien und Herstellungsverfahren, aber die meisten davon sind sehr kostspielig, wie zum Beispiel der 3D-Druck.
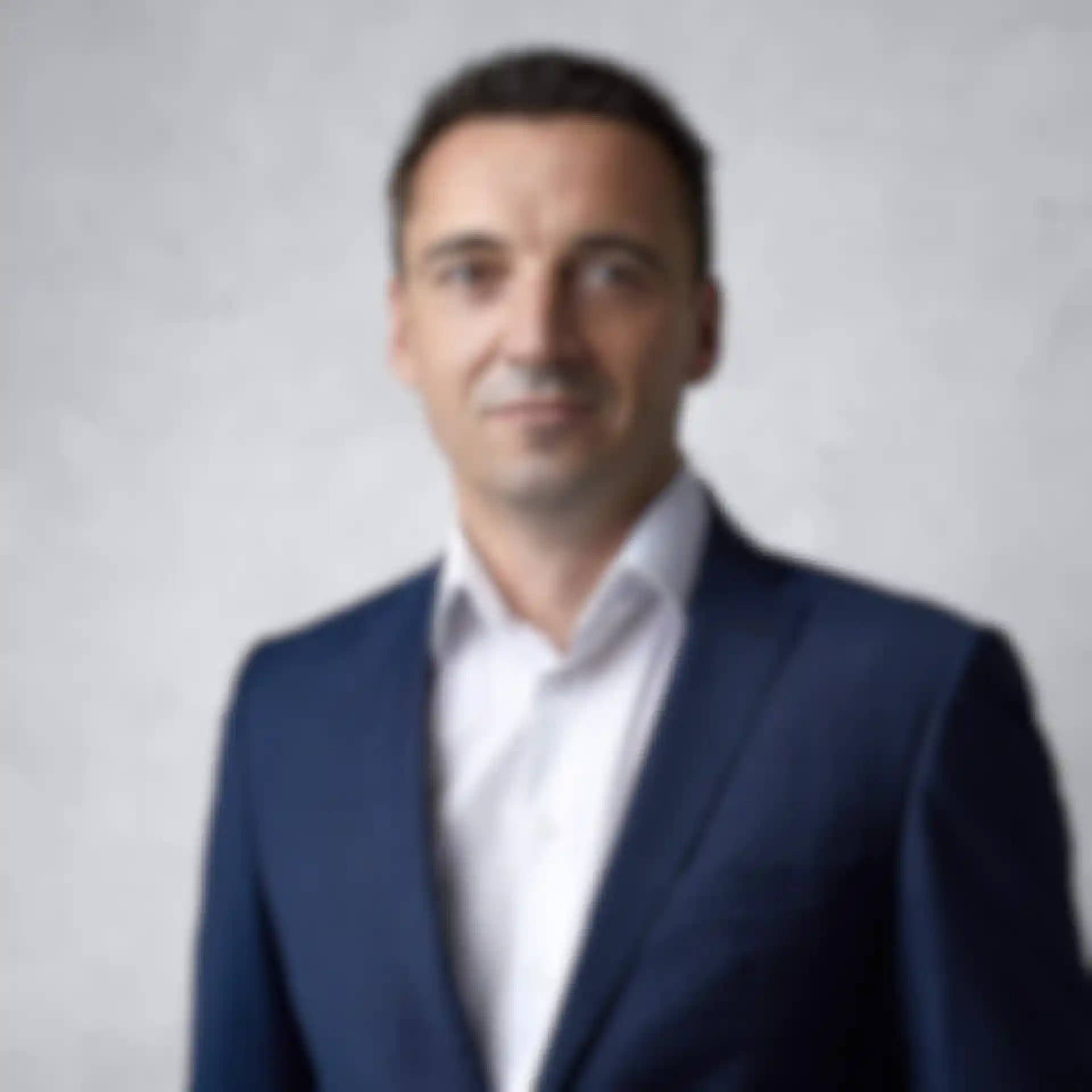
Das ganze Thema kam mir langsam und konservativ vor. Als ich mein Studium beendet hatte, ging ich in den Rennsport, wo der Leichtbau eine zentrale Rolle bei der Konstruktion von Fahrzeugen spielt und für die Aerodynamik wichtig ist, sodass die Kosten nicht so wichtig sind.
Bevor ich mein Unternehmen gegründet habe, habe ich 10 Jahre lang in der Forschung und Entwicklung eines großen Automobilherstellers gearbeitet, und es war eine Herausforderung für mich, meine Erfahrung mit Leichtbau aus dem Rennsport auf die Entwicklung von Bauteilen für die Großserienproduktion zu übertragen. Die Bauteilkosten spielen bei der Herstellung eine sehr wichtige Rolle, sodass die Materialien und Verfahren aus dem Rennsport nicht in Frage kamen.
Es war schon früh klar, dass Leichtbau nur über die Form der Bauteile zu erreichen ist, d.h. sie können nur die notwendigsten Materialien enthalten. Mit Hilfe der Topologieoptimierung kann die ideale Form für die Bauteile gefunden werden, da die Software alle Bereiche, die für die einwirkenden Kräfte nicht relevant sind, aus dem Simulationsmodell entfernt.
Wie bist du darauf gekommen, dass 3D-Software als Teil des Prozesses genutzt werden kann?
Spoida: Zuerst möchte ich erklären, dass Topologieoptimierungen meist sehr organische Formen erzeugen, also stell dir vor, wie die Natur einen Baum wachsen lässt. Es gibt keine rechten Winkel oder scharfen Kanten. Um ein Ergebnis der Topologieoptimierung in ein reales Teil zu verwandeln, muss die das Ergebnis in CAD rekonstruiert werden.
Normalerweise geschieht das mit parametrischer Volumenmodellierung in CAD, aber damit lassen sich die organischen Formen aus der Optimierung nur sehr begrenzt reproduzieren, und man erhält nicht das leichteste Bauteil.
Heutzutage ist Subdivision Modeling in alle CAD-Tools integriert und wird in der Regel als Design- und Stylingfunktion angepriesen, aber unserer Erfahrung nach sind sie nicht so schnell und leistungsstark wie 3D-Modeling-Programme, die für diesen Zweck entwickelt wurden, und sie haben keine Sculpting-Funktion.
Im Allgemeinen arbeiten wir nicht anders als Artists, die 3D-Tools für Games und Filme einsetzen. In unserem Fall muss das Ergebnis der Topologieoptimierung jedoch zunächst interpretiert werden. In den meisten Fällen müssen viele Löcher geschlossen werden, weil sie beim Gießen Probleme verursachen können. Außerdem müssen bestimmte Entformungswinkel eingestellt werden, damit das Teil später aus der Guss- oder Schmiedeform entfernt werden kann.
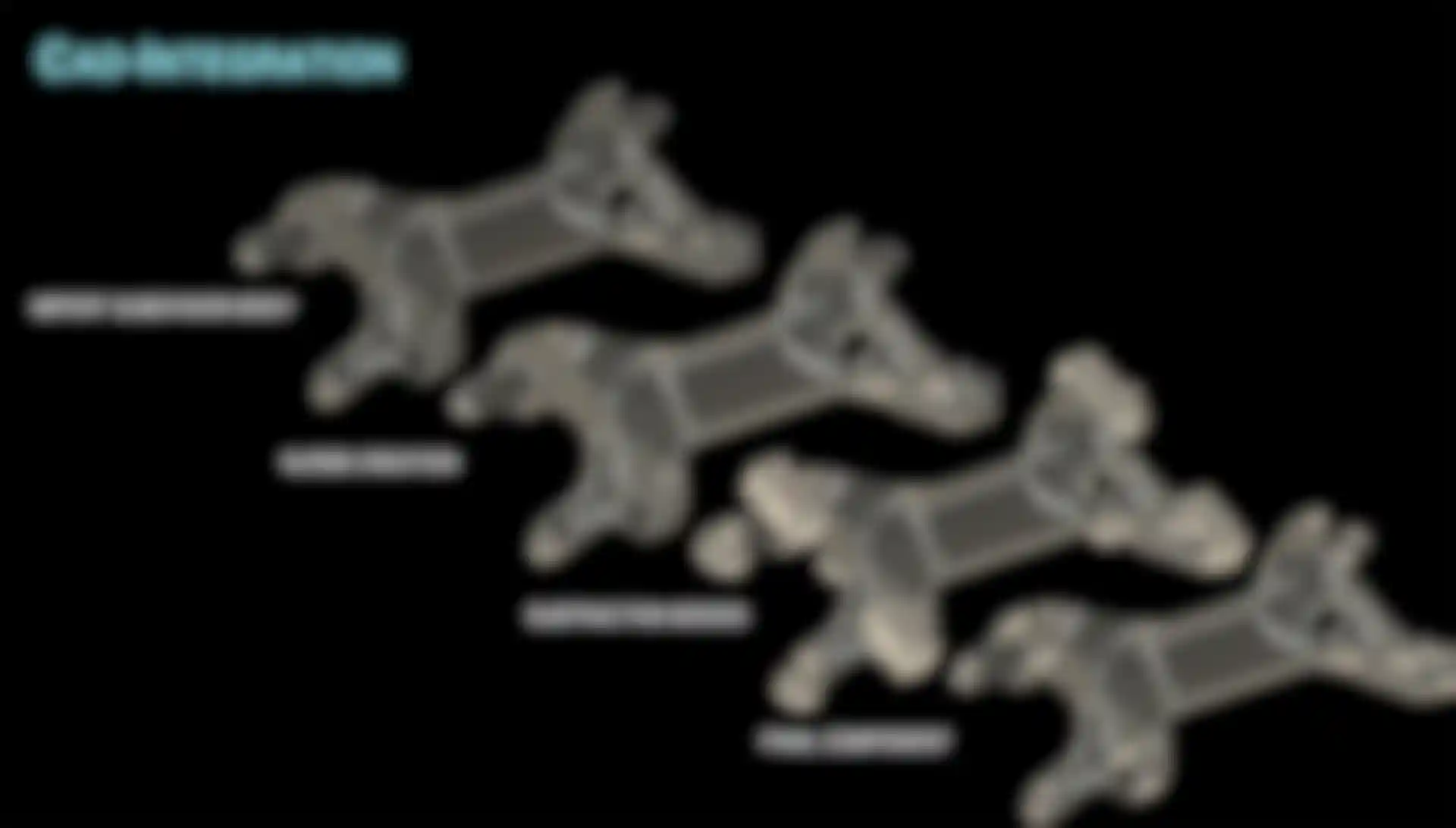
Wir modellieren all diese High-Poly-Modelle in ZBrush mit einer Vielzahl von Sculpting-Pinseln. Wir lernten das 2019, als mein damaliger Arbeitgeber uns erlaubte, nach Los Angeles zu fliegen und uns mit Pixologic zu treffen. Wir verbrachten zwei sehr intensive Tage mit Ofer Alon, Jaime Labelle, Joseph Drust und Paul Gaboury, um über den Einsatz von ZBrush im Engineering zu sprechen.
Das Ergebnis war, dass die Jungs zwei Funktionen, die wir brauchten, in sehr kurzer Zeit implementiert haben, was für uns ein echter Wendepunkt war. Letztendlich geht es immer darum, die Polygonanzahl so gering wie möglich zu halten, denn wir wollen die Subdivisions in CAD importieren und unseren Kunden die Möglichkeit geben, sie in den CAD-Tools für Subdivision Modeling anzupassen.
Erzähle uns etwas mehr darüber, wie Subdivisions einen kontinuierlichen Prozess von der Optimierung bis zur Produktion ermöglichen.
Spoida: Der gesamte Entwicklungszyklus basiert jetzt auf Meshes. Mit der Subdivision-Modellierung können wir den sogenannten Gestaltungsraum innerhalb kürzester Zeit erzeugen. Das heißt, wir füllen den verfügbaren Gestaltungsraum für das zu optimierende Teil. Das geht mit ZBrush sehr bequem, und wir können sicher sein, dass wir wirklich den letzten Winkel genutzt haben, um das leichtestmögliche Teil aus der Optimierung zu erhalten.
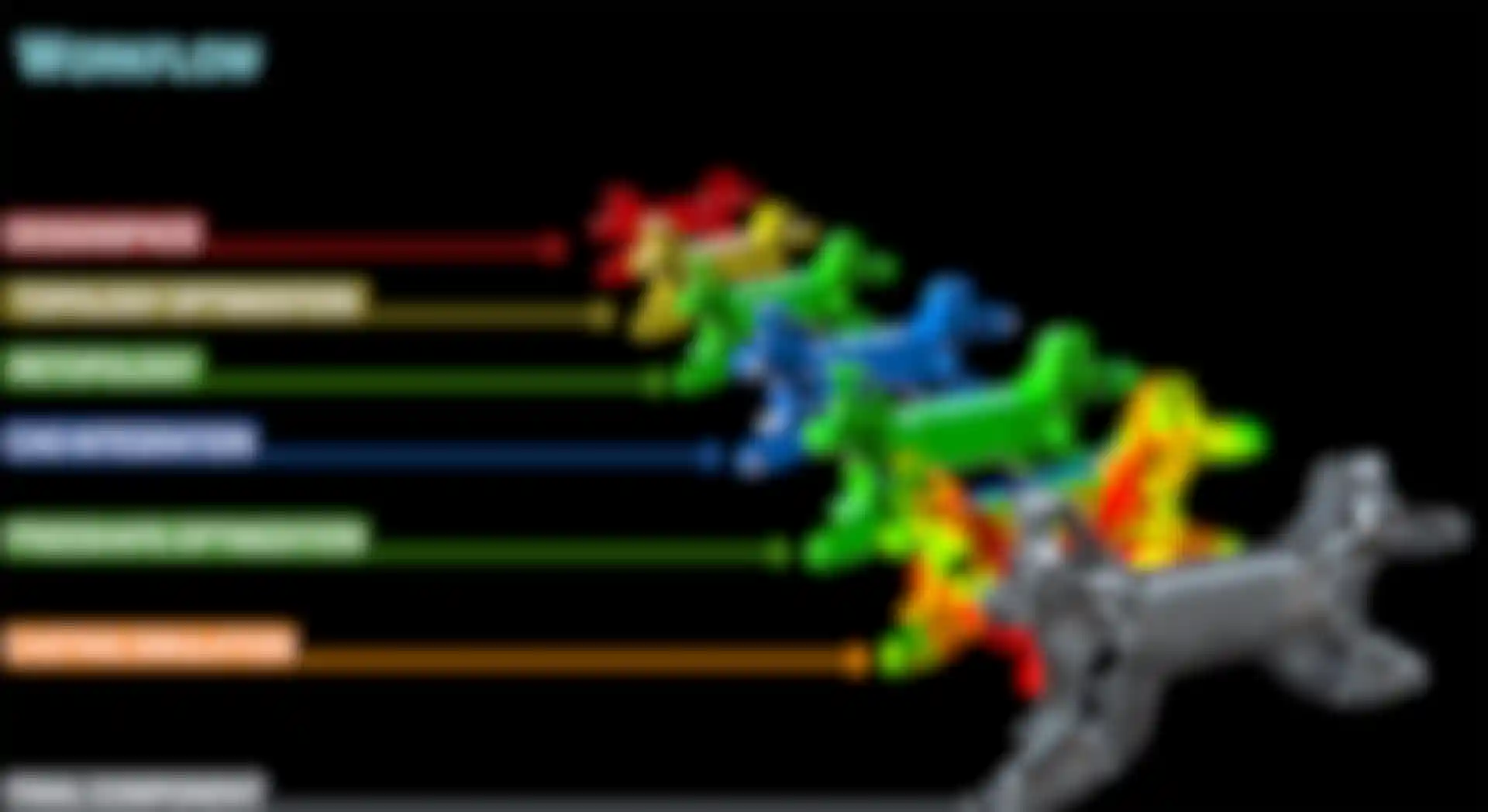
Die Simulation oder Optimierung erfolgt ebenfalls auf Meshes, die keine Polygonmeshes sind, aber von ihnen abgeleitet werden können. Nach der Entwurfsphase geht es an die Herstellung der Bauteile. Neben dem Gießen spielt auch das Schmieden eine große Rolle. Der Zulieferer, der das Bauteil schmiedet, erhält die endgültige Geometrie, die wir als "Rohling" bezeichnen, oder die Geometrie, die vor der Bearbeitung durch Fräsen aus der Schmiede fällt.
Das Schmieden wird nicht in einem Schritt durchgeführt. Es beginnt mit einem dicken, runden Metallzylinder, der in mehreren Schmiedeprozessen zum endgültigen Bauteil wird. Die Geometrien dieser Zwischenschritte müssen normalerweise aufwändig im CAD konstruiert werden, aber die Subdivision-Modellierung macht den Prozess viel schneller und präziser. Im einfachsten Fall wird der SubD-Körper einfach an die endgültige Geometrie angepasst, ohne die Topologie zu ändern.
Welche Auswirkungen hat diese neue Art des Subdivision Modeling auf die Produktion, insbesondere auf die Automobilindustrie?
Spoida: Mit 3D-Modeling-Werkzeugen wie ZBrush können mechanische Teile in extrem kurzer Zeit modelliert werden, und bisher hat der Leichtbau in der Automobilindustrie keine Rolle gespielt. Dank der Topologieoptimierung und der Implementierung von Subdivisions sind wir jetzt in der Lage, extrem leichte Bauteile für normale Massenproduktionsverfahren wie Gießen und Schmieden zu entwickeln.
Je nach Herstellungsverfahren verwenden wir entweder Sculpting in Kombination mit ZRemesher oder wir retopologisieren die Topologie direkt mit ZModeler.
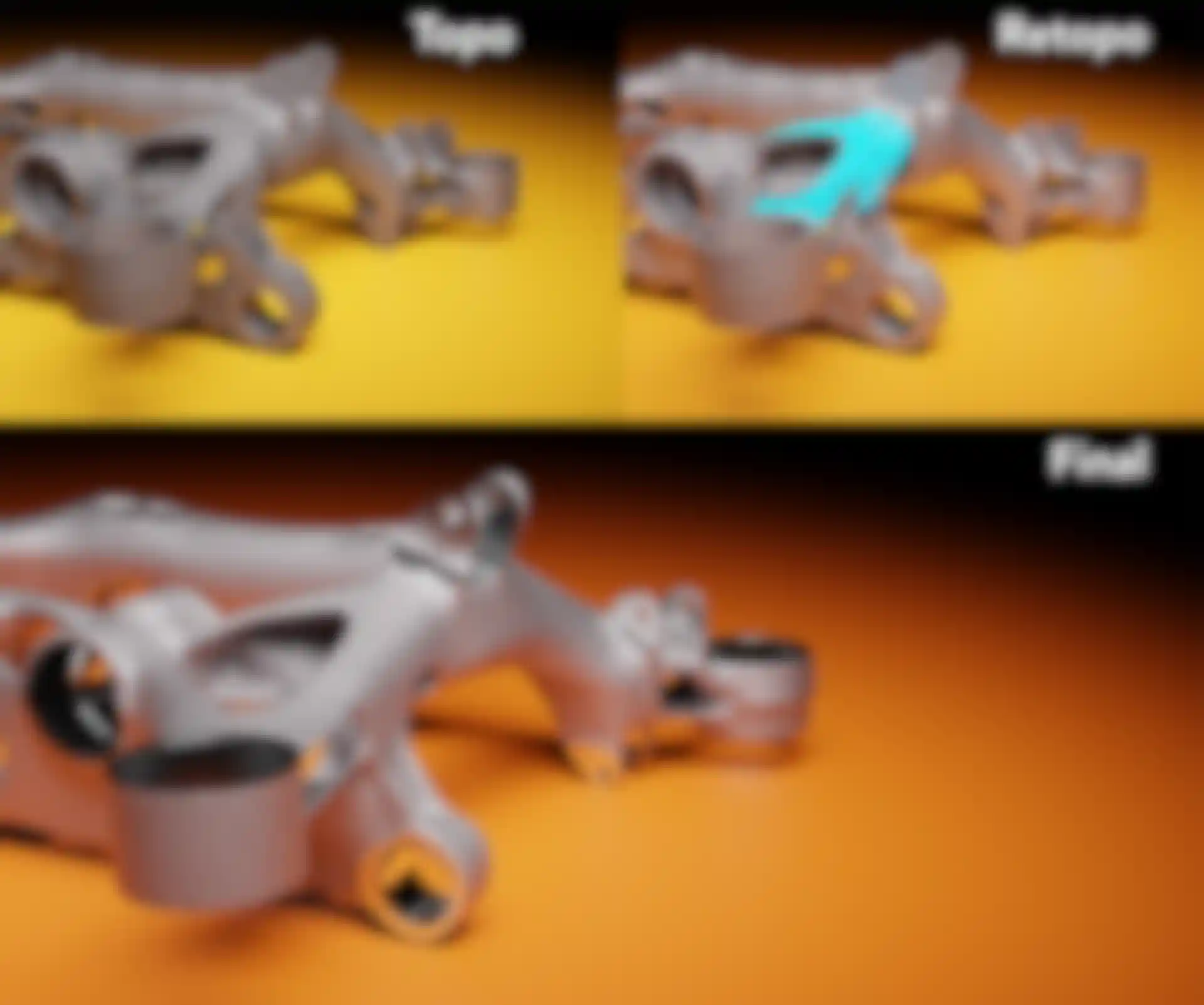
Das ist aus vielen Gründen von Vorteil. Leichtbauteile benötigen weniger Material und sparen so Geld. Wenn wir zum Beispiel ein Gussbauteil optimieren müssen, ändern wir nicht den Herstellungsprozess, sondern reduzieren nur den Materialeinsatz so weit wie möglich, und das schlägt sich in den Bauteilkosten nieder.
In den letzten Jahren ist das Thema Elektromobilität immer wichtiger geworden und gewinnt jetzt an Fahrt. Aber Elektroautos haben Herausforderungen, die Verbrennungsfahrzeuge nicht haben, insbesondere die Frage der Reichweite. Je schwerer das Fahrzeug ist, desto größer ist logischerweise die Masse, die beschleunigt werden muss, was sich direkt auf die Reichweite auswirkt.
Die Batterien sind der wichtigste Faktor für die Reichweite, aber sie sind sehr schwer und man kann nicht beliebig große Batterien einbauen, um mehr Reichweite zu erzielen. Deshalb ist es umso wichtiger, den Rest der Fahrzeugstruktur so leicht wie möglich zu machen. Leichtere Fahrzeuge helfen dabei, wertvolle Energie zu sparen und sind auf Dauer nachhaltiger.
Wie arbeitet Bionic Mesh Design mit den Kunden zusammen?
Spoida: In den meisten Fällen bieten wir den kompletten Service von der Generierung des Gestaltungsraums über die Topologieoptimierung und Retopologie bis hin zur CAD-Integration. In manchen Fällen liefern die Kunden aber auch bereits ein Ergebnis der Topologieoptimierung, das wir nur noch retopologisieren müssen.
Die Automobilindustrie spielt für uns eine große Rolle, aber auch alle anderen Branchen, in denen der Transport eine Rolle spielt, können vom Leichtbau profitieren, z. B. die Schifffahrtsindustrie und die Luft- und Raumfahrt.