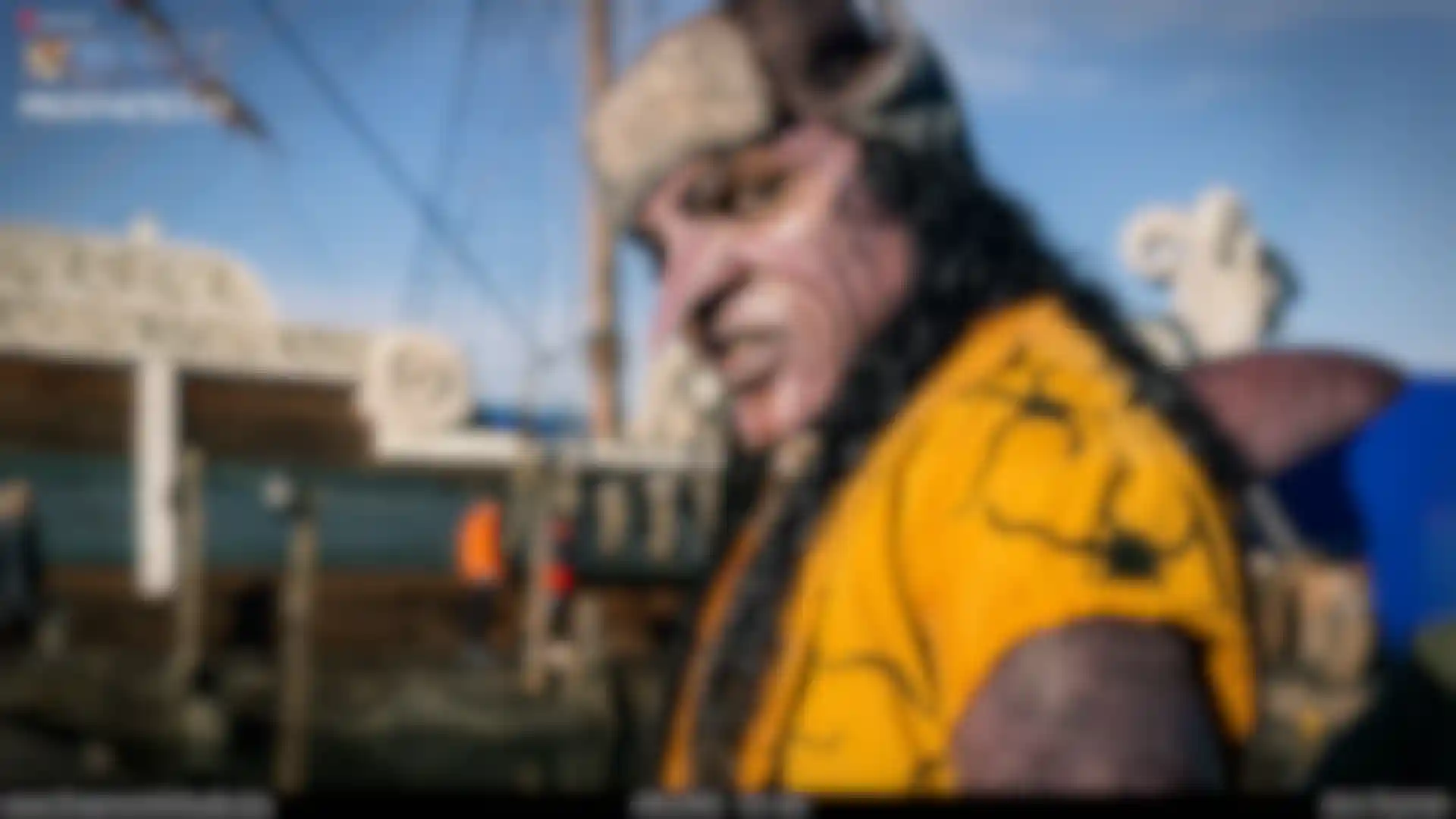
Creating Characters for Netflix’s ‘One Piece’ With ZBrush Prosthetic character designer Jaco Snyman on the workflow behind Arlong, a saw-tooth fish man.
“One Piece”, a live-action adaptation of the best-selling manga series by Eiichiro Oda, for Netflix, is set in a fantastical world populated by humans, animal people, and monsters. The series follows the adventures of the Straw Hat Pirates as they search for the fabled One Piece treasure.
Season One included eight episodes featuring the work of Prosthetic Character Artist Jaco Snyman and his company, Dreamsmith, who are already known for “Mad Max: Fury Road,” and “Raised by Wolves.”
We talked with Snyman and mold maker Mathew Howard-Tripp about their digital workflow that uses ZBrush to develop character concepts, create final sculpts, and design mold systems, allowing the team to 3D print, paint and apply prosthetics to actors. Specifically, we asked how they created the bad-guy character, Arlong, who has a very striking nose.
How did “One Piece” come to you and what was the scope of your work?
Snyman: Our production partner Film Afrika brought us on board. “One Piece” is a unique world with very strange characters that blend animal and human features. We were asked to do all the prosthetic character concepts, sculpting, and mold making for the show, including printing, assembly, casting, painting, fitting, and make-up.
We made about ten full prosthetic characters, including the main bad guy, Arlong, and his two henchmen. We also made pullover masks and more subtle prosthetics, including a metal jaw, goldfish features and rat whiskers for other characters.
How did you approach adapting the manga style for live action?
Howard-Tripp: Early conversations and concepts were about finding the balance between manga and real-world style, as well as hyperrealism and exaggerated, cartoonish features, like the size of fins and gills, a metallic jaw and Arlong’s saw-tooth nose. It helped that Oda-sensei was part of the production team and approved all adaptations and designs.
Describe your process for creating Arlong, the saw-tooth shark man.
Snyman: I sculpted all the characters in ZBrush based on conversations and references in pre-production. It helped that the decision had been made to keep the world and characters human scale. We adapted Arlong’s height and the length of his saw-tooth nose to make him more believable as half human. I did a series of block-out designs to show different options before the actor was cast, and a final look was approved.
As soon as the actor was cast, we got a full 3D body scan of him emailed to us in Cape Town. I based the final digital sculpt with all the prosthetic elements and costume on that data. I used Shane Olson’s 3dcw Fill brush, one of my absolute favorites, to clean up the raw 3D scan files. It averages the surface noise, smoothing out creases next to peaks without destroying the data around it. It’s very good for removing noisy surface texture from the scan while preserving anatomical data, enabling us to make an accurate and life-like representation of what the final character looked like.
To achieve realistic skin on the webbed hands quickly, I transferred skin textures from high-resolution 3D scanned meshes from Ten24 and projected them onto my 3D sculptures using the ZWrap plugin. The webbing texture between the fingers was hand-sculpted in ZBrush.
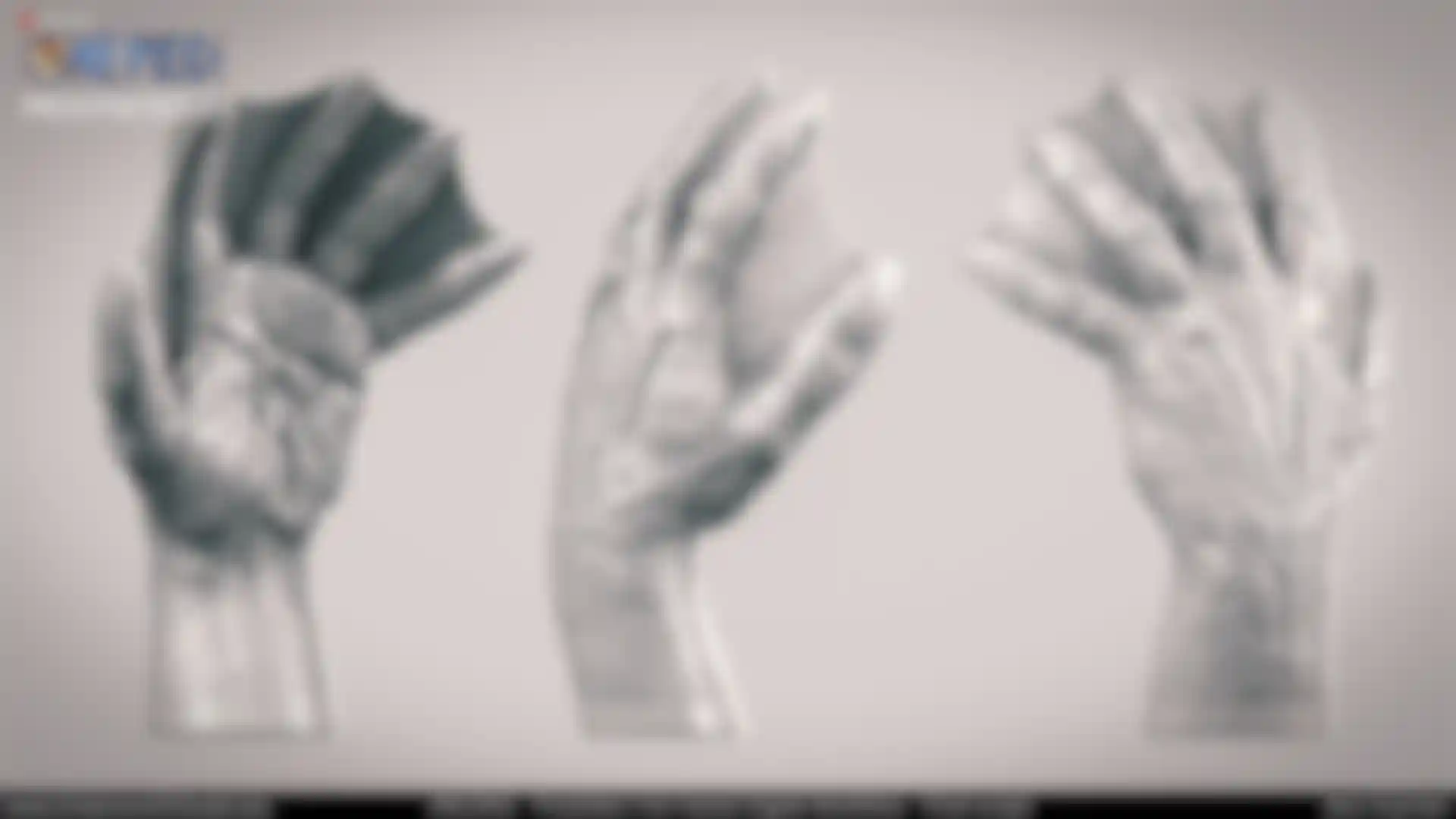
How did you prepare the mold system?
Snyman: After a character was approved, we split the digital sculpture into sections based on the complexity and size constraints of our Formlabs printers. Arlong had three pieces; his face, neck, and extra-long nose, which was glued on during application. The dorsal fin, webbed hands, and creature teeth also had their own molds.
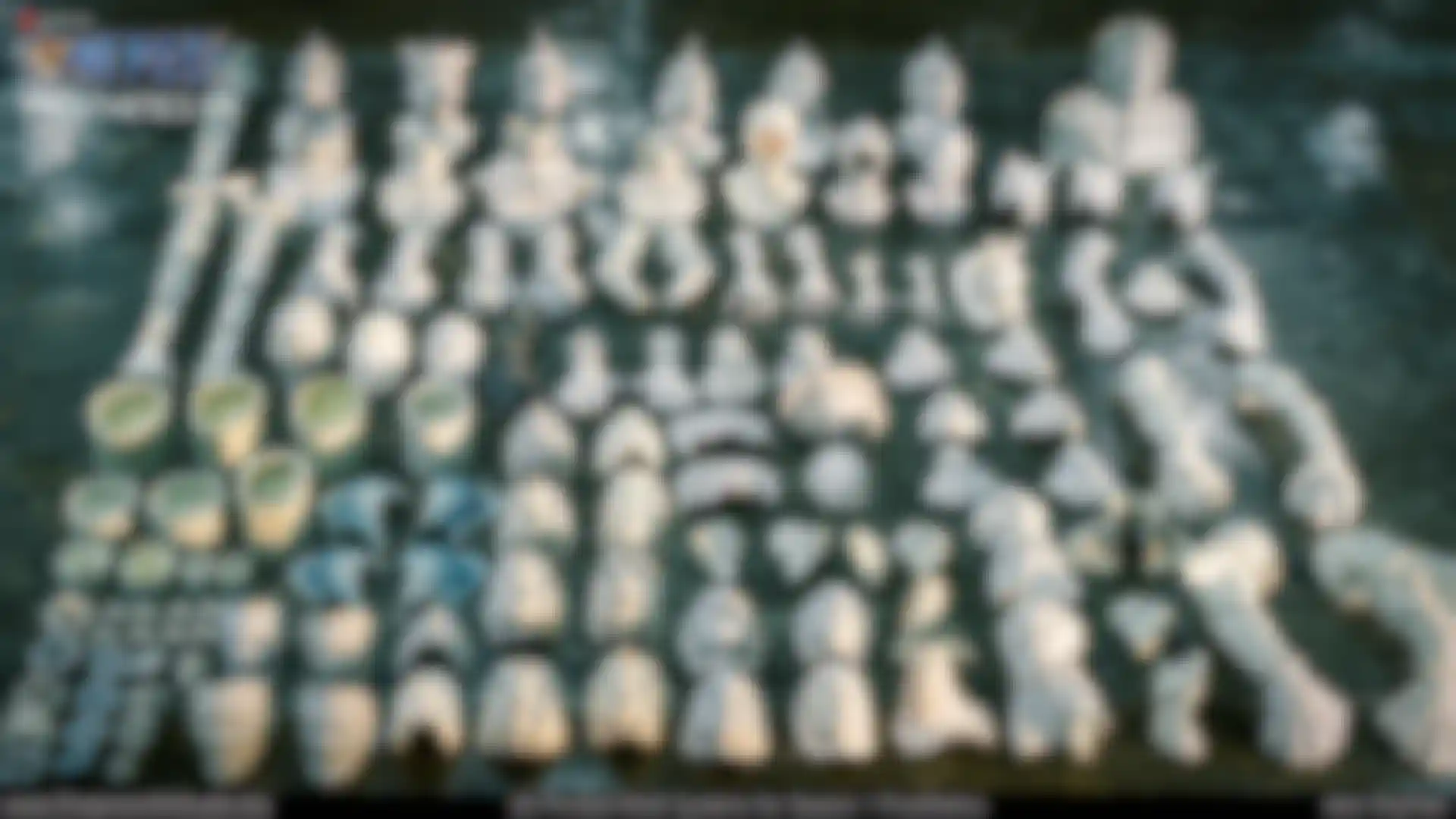
Howard-Tripp: The hard surface tools in ZBrush are incredible for making digital molds. We use the Dynamic feature a lot, where you have a plane that you can add thickness to very easily. For instance, to split the mold into sections, we add a cut line by using a plane that we bend and shape. Then, we hit the Dynamic button to generate thickness to it. Prosthetic appliances are sculpted with paper-thin edges for blending them seamlessly into skin and the Dynamic tool gives us the tolerance control and accuracy we need to achieve this.
To break down the process very simply, I created a string of Boolean operations adding the person’s bust, the sculpt, and all the other relevant information. I subtracted that from a slightly larger version of the same object to create a negative mold with a precise wall thickness.
Then, I carefully split the mold into smaller parts so it could be opened easily once the final prosthetic has been cast. The mold prints over a few days before being cleaned, assembled, and run in the workshop.
Seeing the prosthetic characters on screen, what are you most proud of?
Snyman: It was a big responsibility to do these iconic characters justice for the fans. I think we created believable characters that kept true to the manga and anime worlds. I’m proud of my team and our workflow that supports artists and technicians, especially my on-set crew who had to do countless hours of prosthetic applications to make it all look incredible on camera.
All images courtesy of Netflix.
One Piece Season 1 – Prosthetics Crew List
Jaco Snyman – HOD / Designer
Mathew Howard-Tripp – Digi Moldmaker / Workshop Supervisor
Ashley Powell – Junior Designer / Sculptor
Penny du Plessis – Senior Prosthetic Artist
Natasha du Toit – On Set Supervisor
Zania Gerber – Finisher
Furio Tedeschi – Concept Artist
Steven Saunders – Concept Artist
Megan Wylie – Prosthetics Assistant
Anja Rechholtz – Senior Prosthetics Artist
Margueritte Blom-Briedenhann – Prosthetics Assistant
Joeke Bonthuys – Prosthetics Artist
Lise-Marie Bothma – On Set Coordinator
Peter Goosen – Coordinator / 3D Printer Technician
Richard Woodborne – Mould Maker
Marike Liebetrau-Crause – Prosthetic Artist
Jessica Nixon – Prosthetics Assistant
Richard Grimm – Workshop Technician
Andy Huang – Junior Prosthetic Artist
Monde Mambinga – Mold Maker
Yvonne Muringani – Junior Technician
Nicole Roxburgh – Prosthetics Assistant
Rick Woodborne – Junior Prosthetics Assistant
Michaela Young – Prosthetics Artist
Jonathan Baartman – Junior Mold Maker
Keitumetse Cindi – Prosthetic Assistant
Helena Swahn is a writer in London, UK.